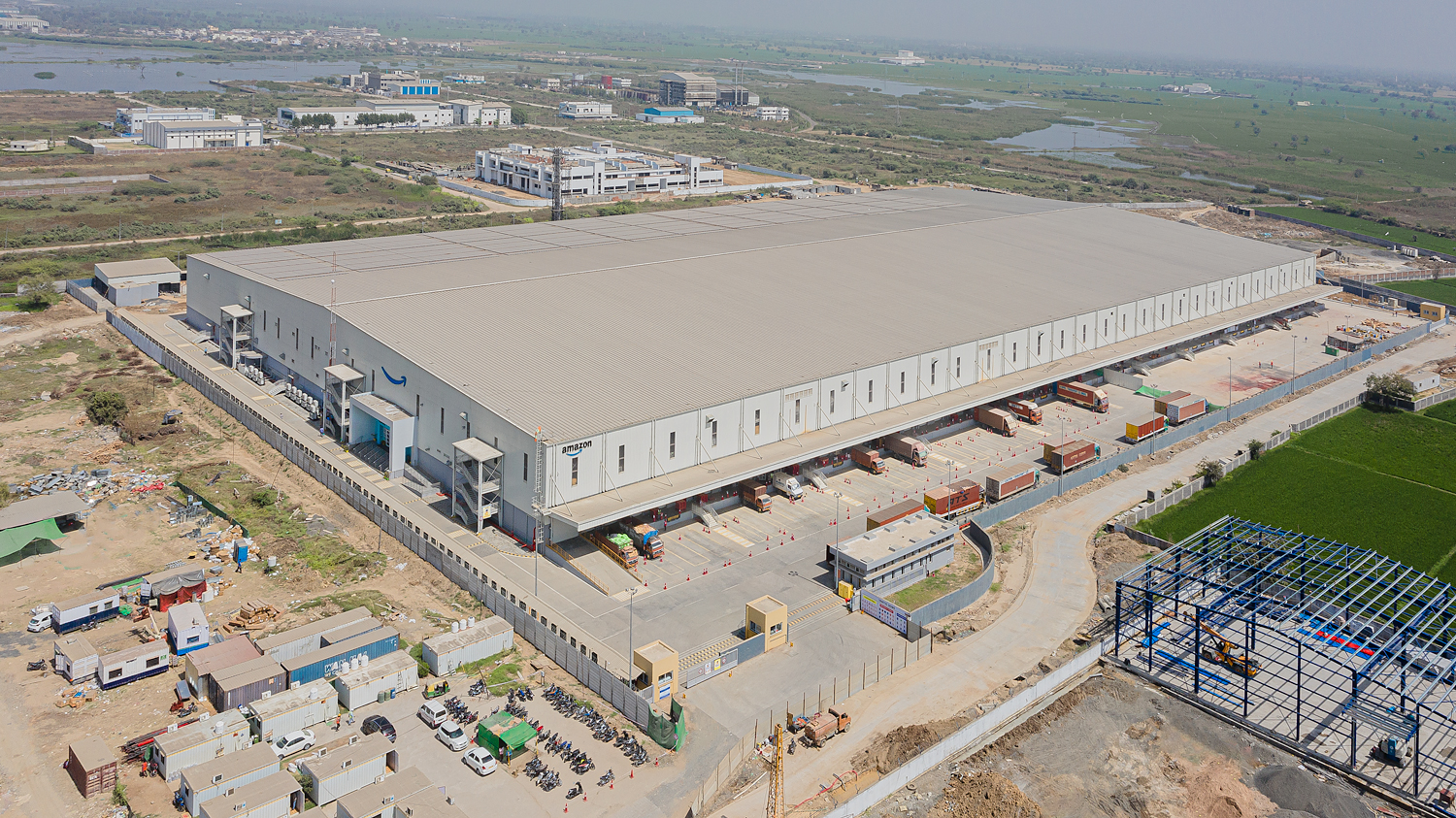
Planning Factors for Material Flows and Logistics: The Essence of Industrial Architecture and Facility Planning
General Introduction
In the dynamic landscape of modern manufacturing, efficiency and productivity are paramount. One of the critical elements that play a pivotal role in achieving these goals is the planning of factories for material flows and logistics. This area of industrial architecture and facility planning may seem inconspicuous, but it forms the very backbone of any successful manufacturing operation. In this article, we will be focusing on the key considerations and strategies that underpin the planning of factories for optimal material flows and logistics.
The Nexus of Material Flows and Logistics
Before we dive deep into the intricacies of factory planning, it is essential to understand the interplay between the flow of materials and logistics. Material flows refer to the movement of raw materials, work-in-progress, and finished products within a manufacturing unit. Logistics, on the other hand, encompasses the broader horizon of supply chain management, including transportation, warehousing, and distribution.
The seamless integration of these two elements is vital for an efficient and cost-effective manufacturing process. A systematically planned factory space optimizes material flows to reduce waste, minimize production lead times, and improve overall production efficiency. This synergy ensures that the right materials are in the right place at the right time, resulting in a lean and agile manufacturing operation.
The Foundation of Effective Factory Planning
1. Layout Design:
The physical layout of a manufacturing space is fundamental to the efficiency of material flows and logistics. Different layouts, such as process, product, and cellular layouts, have diverse implications for the movement and handling of materials.
- Process Layout: This layout arranges machines and workstations according to the type of operation they perform. While it can be suitable for certain industries, it may lead to long material transfer distances and increased handling in others.
- Product Layout: Also known as a line or flow layout, it arranges machines and workstations in a linear sequence, ideal for high-volume production of standardized products. It minimizes material handling and streamlines logistics.
- Cellular Layout: This layout groups machines and workstations into cells, each responsible for a specific product or product family. It combines the advantages of both process and product layouts by reducing material handling and promoting flexibility.
Choosing the right layout is a crucial decision in factory planning as it directly impacts material flows and logistics efficiency.
2. Material Handling Systems:
Efficient material handling systems are the arteries of a well-planned factory. Conveyor systems, automated guided vehicles (AGVs), and robotic systems are examples of technologies that can streamline the movement of materials within the facility. These systems reduce manual handling, minimize errors, and accelerate material transfer, thus enhancing overall logistics efficiency.
3. Inventory Management:
Effective inventory management plays a pivotal role in material flows and logistics. Maintaining optimal levels of raw materials, work-in-progress, and finished products ensures that production is not hampered due to shortages or excessive inventory costs. Modern inventory management systems and technologies, such as RFID and barcoding, provide real- time visibility and control over inventory, contributing to streamlined logistics.
4. Demand Forecasting and Planning:
Accurate demand forecasting is essential for planning material flows and logistics. A clear understanding of future demand enables manufacturers to optimize production schedules, plan for transportation, and align warehouse operations accordingly. Leveraging data analytics and forecasting tools can provide valuable insights for proactive planning.
5. Transportation and Distribution:
While factory planning primarily focuses on the internal aspects of material flows, it is essential to integrate external logistics into the equation. Efficient transportation and distribution networks ensure that materials are sourced and products are delivered on time. Factors like choice of transportation mode, route optimization, and distribution center locations are critical for achieving this synergy.
The Role of Technology in Factory Planning
In recent years, technological advancements have revolutionized factory planning for material flows and logistics. Here are some key technologies that are shaping the future of industrial architecture and facility planning:
1. Internet of Things (IoT):
IoT sensors and devices are increasingly used to monitor the movement and condition of materials within a factory. These sensors provide real-time data on material location, temperature, humidity, and other relevant parameters, enabling better control and decision- making.
2. Artificial Intelligence (AI) and Machine Learning:
AI and machine learning algorithms are employed to optimize material flows and logistics. They can predict demand patterns, suggest efficient routing for materials, and even control automated material handling systems to adapt to changing conditions.
3. Warehouse Management Systems (WMS):
WMS software helps manage inventory within warehouses efficiently. It provides real-time visibility into stock levels, facilitates order picking, and optimizes storage, enhancing logistics within the factory.
4. Digital Twins:
Digital twins create virtual replicas of factories, enabling manufacturers to simulate and test different layouts and material flow scenarios before implementing them in the real world.
This technology minimizes the risks associated with facility planning changes.
The Sustainability Imperative
In today’s environmentally conscious world, sustainability is an integral aspect of factory planning for material flows and logistics. Sustainable practices not only reduce the ecological footprint but also often result in cost savings and enhanced brand reputation. Here are some strategies for incorporating sustainability into factory planning:
1. Energy-Efficient Design: Optimize the factory layout and equipment for energy efficiency. Incorporate natural lighting, invest in energy-efficient machinery, and implement energy management systems.
2. Reducing Waste: Minimize waste generation within the manufacturing process. Implement recycling programs and explore ways to reuse materials whenever possible.
3. Green Transportation: Choose eco-friendly transportation options and optimize transportation routes to reduce carbon emissions.
4. Environmental Regulations Compliance: Stay abreast of environmental regulations and ensure that the factory’s design and operations comply with them.
Wrapping Up
Factory planning for material flows and logistics is an art and science that requires a deep understanding of manufacturing processes and technology and a keen eye for efficiency. A well-planned factory not only enhances productivity but also provides a competitive edge in a globalized market. As technology continues to advance, manufacturers must adapt and embrace the latest innovations to remain agile and responsive in an ever-evolving landscape.
In the pursuit of excellence, industrial architects and facility planners are tasked with shaping the future of manufacturing by optimizing material flows and logistics. By integrating technology, sustainability, and best practices, they can create factories that are not only efficient but also environmentally responsible—a testament to the power of effective factory planning in the modern industrial era.