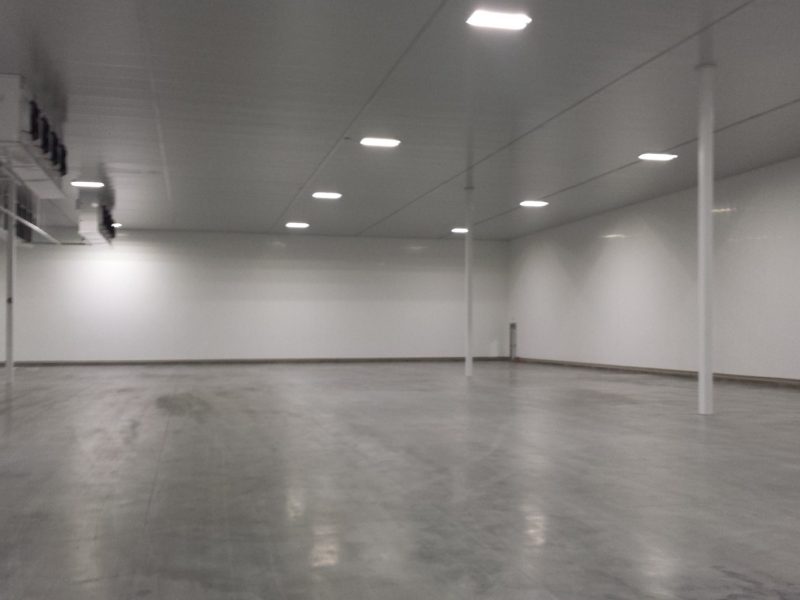
Criterias for selecting wall panels and its types for food and pharma facilities
Selecting the appropriate wall panels for food and pharmaceutical facilities is a crucial choice that profoundly affects the overall operation, cleanliness, and safety of these establishments. In order to maintain product quality and consumer safety, these industries must adhere to strict regulations and standards.
Criteria for Selecting Wall Panels:
1. Hygiene and Cleanability:
Choosing the right wall panels for food and pharmaceutical facilities is a key decision that can have a big impact on the entire operation, hygiene, and safety of these places. To maintain product quality and consumer safety, these sectors adhere to severe laws and standards. In this comprehensive guide, we will look at the criteria for choosing wall panels as well as the numerous types that are available for these particular buildings.
2. Chemical Resistance:
These industries commonly employ severe cleaning and disinfecting treatments. To ensure long-term endurance, wall panels should be resistant to certain substances. Preferably, panels composed of stainless steel, FRP, and chemically resistant polymers
3. Compliance with Regulations:
Food and pharmaceutical facilities are subject to stringent regulatory standards such as FDA (Food and Drug Administration), cGMP (Current Good Manufacturing Practice), and HACCP (Hazard Analysis and Critical Control Points) (Hazard Analysis and Critical Control Points). Wall panels must meet these specifications in order to ensure product safety and quality.
4. Moisture Resistance:
Moisture and humidity are common in food processing and pharmaceutical manufacturing environments. Moisture-resistant wall panels are required to avoid mold, bacterial growth, and structural damage. FRP, PVC, or specific moisture-resistant coatings are all viable options.
5. Temperature Control:
Temperature control is critical in pharmaceutical manufacturing and some food processing applications. Insulated wall panels can assist in establishing and maintaining temperature control.
6. Durability:
The chosen wall panels should be strong enough to resist the operational needs of the facility. They must be resistant to physical impact, abrasion, and the wear and tear that is common in these industries.
7. Fire Resistance:
Fire-resistant wall panels may be necessary to improve safety and prevent the spread of flames, depending on the unique needs and local construction codes. There are special fire-rated panels available for this purpose.
8. Aesthetics:
While utility and safety are the most important considerations, aesthetics can also be important, especially in places that are visible to clients, visitors, or inspectors. Wall panels are available in a variety of colors, coatings, and designs to complement the facility’s design and branding.
Types of wall panels:
1. FRP (Fiberglass Reinforced Plastic):
Because of their longevity, moisture resistance, and simplicity of cleaning, FRP panels are a popular choice. They are appropriate for both food and pharmaceutical operations, particularly in regions where hygiene is essential.
2. Stainless Steel:
The corrosion resistance and durability of stainless-steel panels are well recognized. They are appropriate for locations requiring great cleanliness and frequent cleaning with strong chemicals, such as cleanrooms and sterile manufacturing environments.
3. PVC (Polyvinyl Chloride):
PVC wall panels are a low-cost choice for locations where chemical protection is required. They are also simple to clean, making them ideal for use in food processing plants.
4. Composite Panels:
Composite panels mix elements such as aluminum, foam, and steel to provide insulation, durability, and structural integrity. These can be employed in temperature-controlled facilities.
5. HPL (High-Pressure Laminate):
HPL panels are used for their simplicity of cleaning and aesthetically pleasing appearance. They are appropriate for locations that must retain a visually appealing look while adhering to cleanliness regulations.
6. Acrylic Panels:
Acrylic panels are utilized in situations where cleanliness and appearance are crucial, although they may not be as long-lasting as other solutions. They provide transparency as well as visual appeal.
7. Gypsum Board with Special Coatings:
For non-critical portions of these buildings, gypsum board panels with particular moisture-resistant or chemical-resistant coatings can be a cost-effective option.
In conclusion, selecting wall panels for food and pharmaceutical facilities is a difficult decision that must consider cleanliness, compliance, chemical and moisture resistance, durability, temperature control, fire safety, and aesthetics. Depending on the demands of the facility, a mix of numerous panel types may be employed to meet many purposes within the same area.
Working closely with facility design and compliance professionals is crucial to ensure the optimal wall panel selection for each area of the facility, assuring product safety and quality in the end.