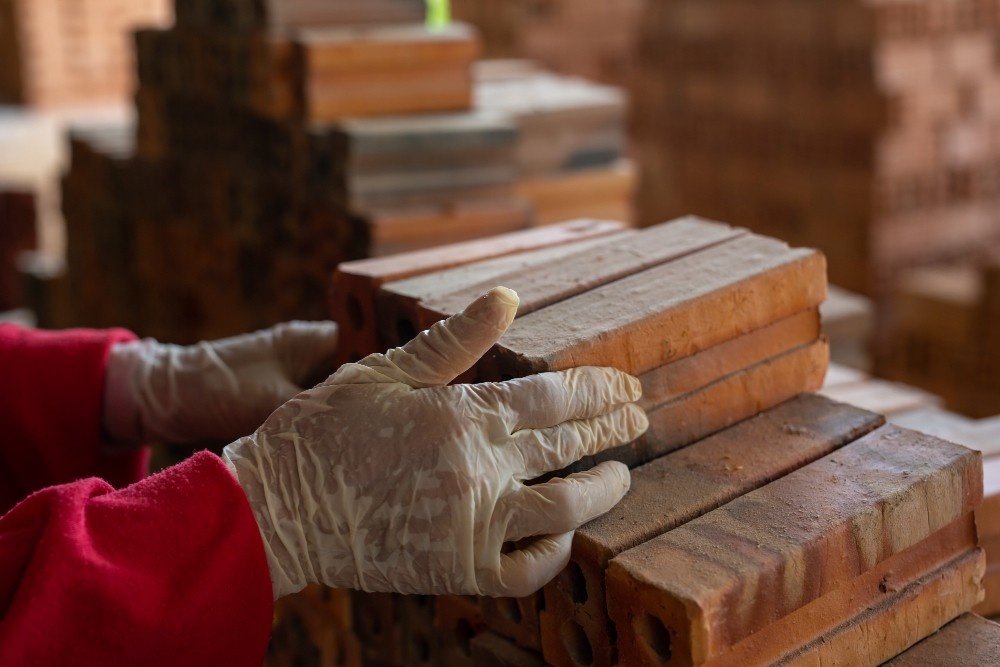
Are Traditional Materials Still Relevant in the Future of Factory Design?
In industrial infrastructure, concrete and steel have long been synonymous with factory construction for decades. As construction practices become more sustainable and efficient, new materials are emerging that deliver advantages in terms of cost-effectiveness, environmental impact, and operational efficiency. These materials are redefining the way factories are built, designed, and operated.
Here we explore some of the latest developments in materials for factory construction, how they benefit the industry, and how they can be applied to the Indian context.
Why Move Beyond Concrete and Steel?
Steel and concrete have been staples of industrial construction because of their strength, durability, and versatility. Although these materials are widely used, they pose significant environmental and logistical challenges. Concrete, for instance, contributes heavily to global CO2 emissions, and steel production consumes a great deal of energy and raw materials.
In recent years, we have seen a growing demand for more sustainable, energy-efficient, and cost-effective alternatives. This has led to new materials being explored and adopted, offering solutions better suited to today’s environmental goals in the manufacturing and construction sectors.
What Are the Latest Material Innovations in Factory Construction?
1. Cross-Laminated Timber (CLT)
Cross-laminated timber (CLT) is one of the biggest innovations in building materials today. This engineered wood product is made by layering pieces of wood at different angles to make it stronger and more stable. CLT is not only a sustainable alternative to steel and concrete, but it also has a smaller carbon footprint.
Advancements in CLT technology have allowed it to be used in more complex and larger structures, such as industrial buildings. With its lightweight properties, easy handling, and excellent insulation properties, CLT makes an excellent building material for energy-efficient factories. Additionally, CLT’s carbon sequestration properties, which allow the wood to absorb and store carbon dioxide, make it a more environmentally friendly choice for modern industrial construction.
2. Transparent Concrete
Transparent concrete, also known as light-transmitting concrete (Litracon), is a material that combines traditional concrete with optical fibers to create a concrete surface that can transmit light. While still relatively new in factory construction, transparent concrete is gaining attention due to its aesthetic appeal and energy-efficient properties.
In factory construction, transparent concrete can be used to incorporate natural light into production areas, reducing the need for artificial lighting during the day.
3. Recycled and Upcycled Materials
As sustainability becomes more important, the use of recycled and upcycled materials is on the rise in factory construction. Recycled concrete, reclaimed wood, and upcycled steel are being used to reduce waste and lower the carbon footprint of construction projects.
Recycled concrete, for example, is made by processing waste concrete from demolished buildings. This material can be reused in new constructions, which not only reduces waste but also decreases the need for new raw materials, making it a cost-effective and environmentally friendly option.
Upcycled materials, such as recycled metal or plastic, can also be incorporated into factory construction. These materials offer durability, resistance to corrosion, and a sustainable alternative to traditional materials, helping to build factories that are both resilient and eco-friendly.
4. Aerated Concrete (AAC)
Autoclaved aerated concrete (AAC) is a lightweight, durable, and energy-efficient building material. It’s made by mixing a combination of sand, lime, water, and an aerating agent to create a material that’s light yet strong. AAC has excellent thermal insulation properties, making it ideal for use in hot climates, such as India.
AAC can be used for walls, floors, and roofs, offering significant energy savings for factory buildings by reducing the need for air conditioning. The material’s fire resistance and sound insulation properties also make it a good choice for factories where safety and noise control are important considerations.
5. Self-Healing Concrete
Self-healing concrete is an innovative material that has the ability to repair its cracks automatically. This is achieved through the incorporation of bacteria or other chemical agents into the concrete mix. When cracks form, these agents are activated, producing a chemical reaction that fills the cracks and prevents further damage.
The benefits of self-healing concrete in factory construction are significant. It extends the lifespan of buildings, reduces maintenance costs, and ensures that factories remain safe and structurally sound. While still in the development phase, self-healing concrete has the potential to revolutionize the durability of industrial structures.
6. 3D Printed Concrete
3D printing technology is revolutionizing construction, including factory buildings. 3D-printed concrete allows for the rapid, precise, and cost-effective creation of factory structures. This method of construction uses a computer-controlled printer to lay down layers of concrete, creating complex designs that would be difficult or impossible with traditional methods.
One of the most significant advantages of 3D printing in factory construction is its ability to reduce waste.
How These Materials Benefit Factory Construction
Sustainability and Reduced Carbon Footprint
The primary benefit of using these innovative materials is their sustainability. Materials like CLT, transparent concrete, and recycled materials help reduce the carbon footprint of factory construction.
Additionally, materials like AAC and self-healing concrete reduce the long-term environmental impact of factory buildings by improving energy efficiency and reducing maintenance needs.
Cost-Effectiveness
While some of these materials may have higher initial costs, they can lead to substantial savings over time. For example, CLT and AAC offer energy savings through better insulation, while recycled materials reduce material costs.
Moreover, self-healing concrete and 3D-printed structures require less maintenance and labor, leading to lower long-term expenses.
Enhanced Worker Comfort and Safety
Materials like transparent concrete can enhance worker comfort by allowing natural light to enter production areas. This can lead to higher productivity and fewer energy costs.
Additionally, materials with excellent insulation properties can create a more comfortable and safe working environment by controlling temperature and reducing noise.
How Can Indian Factories Benefit from These Innovations?
India, with its rapidly expanding industrial sector, stands to gain significantly from these material innovations. By adopting sustainable and energy-efficient materials, Indian factories can reduce their environmental impact and operating costs while meeting the growing demand for green buildings.
The Indian government has already implemented several policies to encourage sustainable construction practices, such as the Energy Conservation Building Code (ECBC) for commercial buildings and the Green Building Rating System. These initiatives make it easier for factories to integrate innovative materials and technologies into their designs.
Build Future-Ready Factories with VMS
Building or upgrading a factory with innovative materials will help you achieve greater efficiency, reduce environmental impact, and maximize long-term savings.
If you are looking to build a factory with cutting-edge materials, VMS Consultants can help guide your project with their expertise in engineering, architecture, and project management.
Partner with VMS Consultants to create an energy-efficient and sustainable facility that sets your business up for future success.