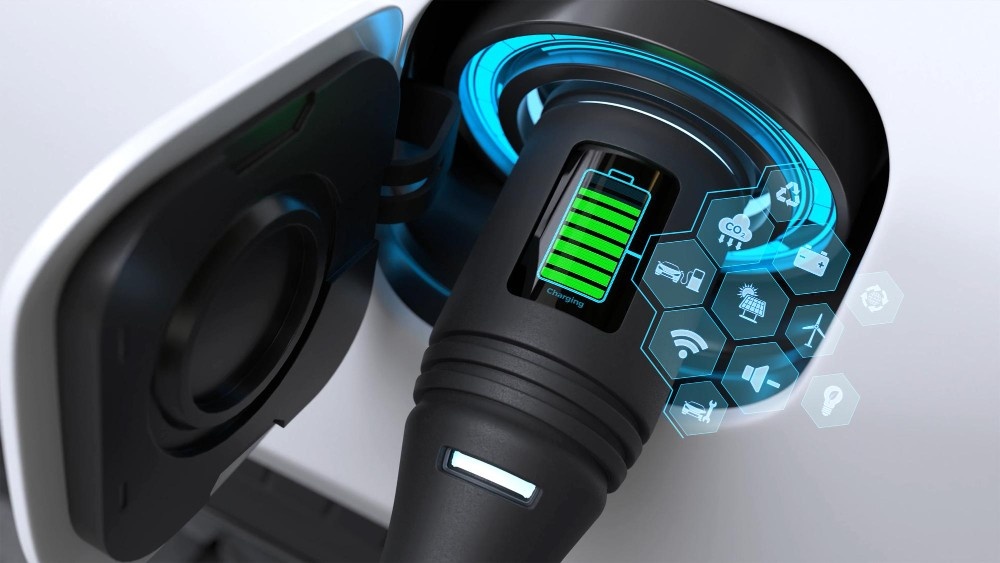
Designing EV Battery Manufacturing Plants: A Comprehensive Guide
EVs are rapidly gaining in popularity across the globe, and one of the critical factors driving this transition is the need for efficient and sustainable battery manufacturing. As the EV market grows, the need for reliable and scalable battery supplies has increased, which has resulted in a rise in the demand for specialized EV battery manufacturing plants.
We will discuss key considerations for building an EV battery manufacturing plant in this article.
Why Are EV Battery Manufacturing Plants Crucial for the Future of Mobility?
Electric vehicle demand is growing around the world due to government incentives, stricter environmental regulations, and climate change awareness.
Having a good battery makes a huge difference in how well an electric car performs, how long it can go, and how much it costs. The EV industry can’t grow as fast as it needs without the capacity to manufacture batteries at scale.
What Are the Key Considerations in Designing EV Battery Manufacturing Plants?
1. Facility Layout and Workflow Optimization
Having a well-planned facility layout will optimize production workflows and minimize waste. The layout should make it easier to transfer materials, from raw materials to finished products. In an EV battery plant, production involves several stages, including electrode preparation, cell assembly, battery module formation, and final testing.
The design should incorporate the proper allocation of space for each stage of the manufacturing process, ensuring adequate space for storage, assembly lines, quality control, and maintenance. The layout should also consider the need for cleanroom environments, which are essential for maintaining the high-quality standards required in battery production.
2. Adherence to Safety Standards
The manufacturing of batteries also involves the handling of hazardous materials such as lithium, cobalt, and other chemicals. Due to the volatile nature of these materials, safety is a top priority. The plant must be designed to include appropriate safety measures to prevent fire, explosion, or exposure to harmful substances.
Fire suppression systems, explosion-proof enclosures, and ventilation systems to control airborne pollutants are essential. Moreover, the design should ensure employee training and emergency protocols are easy to follow.
3. Sustainability and Environmental Impact
Sustainability is a significant concern in the EV battery industry, not just for the final product but also for the manufacturing process. Designing an energy-efficient battery manufacturing plant can significantly reduce the plant’s overall environmental impact. This includes incorporating energy-saving technologies, recycling systems, and waste management strategies.
Renewable energy sources, such as solar panels or wind turbines, can be integrated into the design to power the manufacturing process.
4. Integration of Automation and Robotics
The integration of automation and robotics improves the efficiency and quality of EV battery production. Automated assembly lines can reduce human error, increase throughput, and lower labor costs.
Robotic systems can be used in tasks such as material handling, cell assembly, testing, and packaging. Automation ensures that the production process is consistent and accurate, meeting the precise quality standards required for EV batteries.
5. Scalability for Future Demand
The EV battery manufacturing industry is expected to grow exponentially in the coming years. A key consideration in the design of these plants is scalability. The facility must be designed with the flexibility to expand production capacity in response to growing demand.
This can be achieved by incorporating modular designs, which allow for easy expansion of production lines. Additionally, the layout should include future-proofing considerations such as additional electrical infrastructure or space for new technologies.
6. Quality Control and Testing Facilities
Battery quality is really important, because any defects can compromise the safety and performance of an electric vehicle. A plant design must include dedicated testing and quality control areas where each battery undergoes rigorous checks.
This includes testing for charge retention, thermal stability, and safety features. Quality control should be integrated at every stage of production, from raw material sourcing to final product testing.
How to Ensure Cost Efficiency in EV Battery Plant Design?
Designing a cost-efficient EV battery manufacturing plant involves finding the right balance between quality, safety, and production capacity. While investing in state-of-the-art equipment, automation, and safety measures can be expensive, they ultimately improve productivity and reduce long-term operational costs.
To keep costs under control, it’s important to choose the right location for the plant, considering factors such as labor costs, access to raw materials, and proximity to transportation hubs. Additionally, adopting energy-efficient practices and sourcing locally can help reduce overheads.
What Role Does Regulatory Compliance Play in Plant Design?
Given the critical nature of the products being manufactured, EV battery plants must comply with a range of local, national, and international regulations. These include safety standards, environmental impact assessments, labor laws, and waste management guidelines.
In India, factories are subject to regulations such as the Factories Act and Environmental Protection Act. International certifications such as ISO 9001 (for quality management) and ISO 14001 (for environmental management) also play a crucial role in ensuring that the plant adheres to global standards.
Build an EV Battery Manufacturing Plant with VMS
The design of an EV battery manufacturing plant is a complex but essential task that involves considering a range of factors. The right planning can ensure that EV facilities meet industry demands while adhering to the highest standards of quality and safety.
As the demand for electric vehicles increases, so too will the need for efficient, reliable, and sustainable battery manufacturing plants. Now is the time to start planning for the future of the automotive industry.
If you’re looking to design and build a cutting-edge EV battery manufacturing plant, VMS Consultants is here to help. We specialize in engineering, architecture, and project management services for industrial facilities. Let us help you turn your vision into a reality with our expert solutions.